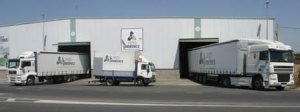
La gestión logística se ha convertido en elemento de carácter estratégico en el mundo empresarial de la actualidad, dentro de la misma se destaca, por su impacto en los clientes e importancia económica, el subsistema de distribución. En la presente investigación se propone un instrumento cuyo principal objetivo es partiendo de un adecuado diagnóstico que incluye elementos geográficos, de tráficos, de tiempo y de costo, favorecer el diseño de sistemas de redes que contribuya a mejorar la efectividad de la distribución física, posibilitando ofrecer un elevado nivel de servicio con el mínimo costo posible para cumplir con los objetivos empresariales y lograr la satisfacción de los clientes.
PROCEDIMIENTO PARA EL DISEÑO DE REDES DE DISTRIBUCIÓN LOGÍSTICA
Sobre la base del estudio de la bibliografía especializada en la materia, donde se consultaron diferentes metodologías para el subsistema de distribución, así como fundamentados en las necesidades de las investigaciones propias de los autores, se desarrolla el presente procedimiento, que consta de 3 fases y 13 pasos.
Fase I: Diagnóstico del sistema de distribución
En esta fase inicial del procedimiento se comienza efectuando un análisis del sistema actual, con el objetivo de conocer las características del sistema objeto de estudio, el cual se tomará como base para el diseño de la red logística.
Paso 1: Inventario del equipamiento actual
Como punto de partida se realiza un levantamiento del equipamiento con que cuenta la organización objeto de estudio, se debe conocer la cantidad de equipos, la descripción de los mismos, su número de identificación, su capacidad dinámica, el consumo de combustible por kilómetro recorrido, además de otros indicadores que se consideren pertinentes para caracterizar el parque de equipos con que cuenta la entidad, con el objetivo de diseñar la red logística.
Paso 2: Obtener información de la organización actual del sistema de distribución
Una vez que se logra inventariar el parque de equipos se procede a obtener información del estado actual del sistema de distribución. El objetivo de este paso es reunir información de los elementos que se consideren importantes a tener en cuenta para el diagnóstico del sistema, se deben aplicar técnicas de recopilación de la información al personal implicado en la actividad logística de distribución, se recomienda consultar a choferes, trabajadores de control de flota, mantenimiento y transporte. Es vital contar con elementos que reflejen por los implicados directos en este proceso su valoración del estado del sistema e identificar los factores susceptibles a mejorar según el criterio de los mismos.
Paso 3: Descripción y análisis de mapas y (o) gráficas del territorio objeto de estudio
Para el diseño de sistemas de distribución, dados sus potencialidades, se ha generalizado el empleo de mapas y (o) gráficas: En este paso se deben emplear para la representación de el(los) origen(es) y el(los) destino(s). En dependencia de la complejidad del sistema de distribución se deben apoyar en ellos para desarrollar el macro y (o) microruteo.
Paso 4: Descripción de la ruta existente
Una vez que ya se tienen ubicados en el mapa el(los) origen(es) y el(los) destino(s), se traza la(s) ruta(s) existente(s), pudiendo realizarse este paso sobre el mapa o en otro formato. De la ruta debe especificarse las distancias entre cada uno de los puntos, por lo que se recomienda elaborar una matriz de distancias, así como describir los puntos y la secuencia del recorrido a través de la construcción de la red logística.
Paso 5: Investigación de la vialidad
Para valorar alternativas se hace necesario efectuar un análisis de la vialidad, con el objetivo de conocer si la ruta que se sigue actualmente es la única posibilidad o si existen otras variantes de acceso para realizar un nuevo diseño de la red de distribución. La vialidad puede ofrecer información para apoyar la toma de decisiones sobre la base de diversos elementos como: los sentidos de las calles, la capacidad permisible de tonelaje transitable y otros que sirvan de fuente de información fiable.
Paso 6: Estudio de tiempos de recorrido
Es muy importante contar con información sobre el tiempo que demora en cada recorrido entre los diferentes elementos que componen la ruta de distribución. Para ello es favorable realizar análisis retrospectivos. En aquellas entidades que cuenten con sistema de GPS se facilita la obtención de datos para efectuar este tipo de estudio, en aquellas que no cuenten con esta tecnología se deberá realizar mediante el análisis de los documentos de los choferes donde describen el tiempo empleado para trasladarse de un punto a otro. Se recomienda elaborar una base de datos para procesar esta información, y aplicar herramientas estadísticas para obtener la descripción de los datos con medidas de tendencia central para el estudio de los tiempos de recorrido.
Paso 7: Estudio de la demanda por segmentos y por clientes
Se debe efectuar un estudio de las necesidades de los clientes, cuantificando su demanda y desglosarla por tipos de productos y(o) servicios. Para ello se debe clasificar si la demanda es regular, o sea, con patrones cuantitativos y cualitativos estables y homogéneos; o si es una demanda irregular donde esos patrones son inestables o heterogéneos. Para estos últimos se considera factible aplicar análisis prospectivos sobre la base de datos por series temporales, para llegar a la proyección de la demanda con márgenes confiables. El objetivo fundamental de este paso es asignar valores fiables de demanda a los clientes, para conocer las necesidades reales de distribución de mercancías.
Paso 8: Estudios de costos
Como último paso de esta fase se culmina con un estudio de costos asociado al sistema de distribución actual. Se cuantifica los gastos asociados a la fuerza de trabajo por concepto de salario, a los medios de trabajo, a través de diversos indicadores económicos como pueden ser gasto de combustible, depreciación, entre otros.
Fase II: Diseño de la red logística
Esta fase es donde se plantean las mejoras al sistema de distribución, sobre la base del diagnóstico se elabora la ruta propuesta y se analiza su factibilidad.
Paso 9: Descripción de la ruta propuesta
Con toda la información analizada en la fase anterior se procede a diseñar la ruta que será propuesta. Los métodos para realizarla pueden ser diversos, los mismos se clasifican en tres grupos: de prueba y error; heurísticos y metaheurísticos; y los denominados de optimización. Los más empleados son los dos primeros, ya que los métodos de optimización no garantizan encontrar la solución exacta en un tiempo razonable de cómputo cuando el número de clientes es grande. Dentro de los métodos de prueba y error se señala como uno de los más utilizados el del Barrido; dentro del los heurísticos se encuentran el Método del agente viajero, Método de los ahorros; Método de emparejamientos y Heurístico de mejora de multirrutas. Dentro de los metaheurísticos se destacan: Algoritmos de hormigas; Programación restringida; Recocido simulado; Algoritmos genéticos; Búsqueda tabú; Tabú granular y el procedimiento de memoria adaptativa. El empleo de programas computacionales ha demostrado ser muy factible para la solución de muchos de esto métodos, por lo que se recomienda su uso en aras de simplificar tiempo y minimizar posibles errores.
Paso 10: Análisis de la factibilidad del diseño
Luego de ser diseñada la ruta por el método seleccionado, se procede a efectuar un análisis de la factibilidad del mismo, donde se deben destacar los elementos de la nueva ruta que demuestran una mejora con respecto al diseño anterior, destacando la distancia y el tiempo de recorrido como variables básicas a analizar, aunque pueden incluirse otros elementos específicos de la organización. Estos análisis en la medida de lo posible deben contener un estudio económico que avale su condición para su diseño e implementación.
Paso 11: Desarrollo del sistema informativo
Como último paso de la fase se recomienda el desarrollo de un sistema informativo que contribuya a facilitar los procesos de captura de datos, procesamiento, análisis, presentación y conservación de la información, como elementos adecuados para el soporte a la toma de decisiones en torno al sistema de distribución.
Para el desarrollo del mismo se deben identificar los sujetos, objetos y medios del sistema informativo. Se pueden emplear las herramientas informáticas más favorables de acuerdo a las características de la empresa y(o) su tecnología implementada.
Fase III: Implementación de la red logística
Como última fase del procedimiento se propone la implementación de la red logística diseñada. El éxito de la misma puede depender en gran medida de los factores inhibidores que imponen las barreras para el cambio, dadas por el querer, poder (que implica el saber y el tener) y el querer cambiar.
Paso 12: Implementación de la nueva red logística
Para la implementación de la nueva red logística se propone realizarla a través de sesiones donde intervengan todos los implicados en el proceso de distribución, desde la alta gerencia hasta los choferes, comunicándoles la factibilidad del nuevo diseño, en aras de darle un tratamiento al cambio y minimizar los efectos resistentes.
Una vez realizado este proceso se debe trazar un plan de acción con hitos temporales, para asegurar la correcta implantación del diseño, definiendo las acciones, los responsables, las fechas de cumplimiento y los indicadores de medida.
Paso 13: Medición y análisis
Como paso concluyente del procedimiento se propone el monitoreo y análisis del nuevo sistema con el objetivo de evaluar los resultados de la red logística implementada para la mejora continua del sistema de distribución.
CONCLUSIONES
El procedimiento propuesto contribuye a perfeccionar el desempeño organizacional a través de un efectivo diseño de redes de distribución física que posibilita ofrecer un elevado nivel de servicio con el mínimo costo posible para cumplir con los objetivos empresariales y lograr la satisfacción de los clientes. El mismo posibilita un adecuado diagnóstico que incluye elementos geográficos, viales, de tiempo y de costo que avalan la factibilidad del diseño propuesto. Se considera que el presente procedimiento es ampliamente generalizable a cualquier tipo de organización, aunque cobra especial importancia en aquellas dedicadas a la distribución de mercancías.
—-
Si quieres mejorar tu conocimiento en TRANSPORTE Y DISTRIBUCIÓN conoce: Técnico Laboral por Competencias en Gestión del Transporte y Distribución.